Description
What is Nickel Alloy Inconel 718 Pipes And Fittings?
Nickell Alloy Inconel 718 Pipe is a nickel-chromium alloy pipe containing niobium and molybdenum, renowned for high strength, corrosion/oxidation resistance, and thermal stability up to 1300°F (704°C). Used in aerospace, oil/gas, and chemical industries under extreme conditions. Manufactured via seamless/welded processes, heat-treated to meet ASTM/ASME standards.
Nickel Alloy Inconel 718 Pipe Fittings are Ni-Cr alloy components with Nb and Mo, offering high strength, corrosion/oxidation resistance, and thermal stability up to 1300°F (704°C). Designed for extreme environments (aerospace, oil/gas), they connect piping systems per ASTM/ASME standards, solution-treated and aged.
Nickel Alloy Inconel 718 Pipes And Fittings Performace:
Nickel alloy Inconel 718 pipes and fittings is a precipitation-enhanced nickel-based high temperature and high strength alloy
Nickel Alloy Inconel 718 Pipes and Fittings exhibit excellent comprehensive properties within the temperature range of -253°C to 700°C, with yield strength below 650°C ranking highest among wrought superalloys.
The material demonstrates superior resistance to fatigue, radiation, oxidation, and corrosion, combined with excellent processability and weldability
Its long-term microstructural stability enables the fabrication of complex-shaped components, meeting stringent requirements in aerospace, nuclear energy, and oil industries.
The alloy’s sensitivity to thermal processing allows precise control of precipitation phases (e.g., γ” phase), achieving optimal mechanical performance through customized heat treatments.
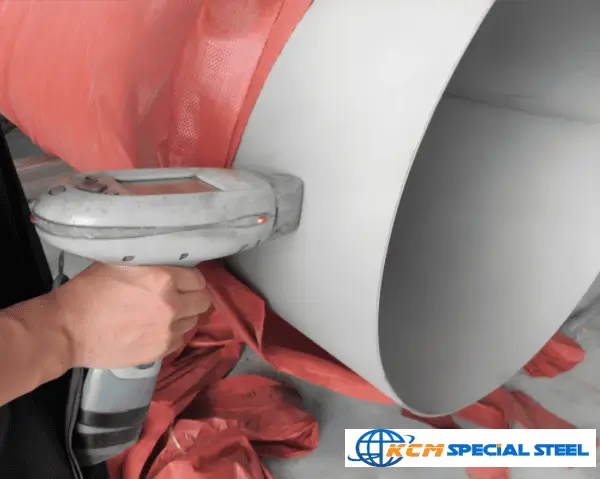
ASTM B670 UNS N07718 Nickel Alloy Inconel 718 Pipes & Fittings Suppliers and Manufacturers in china, ASTM B366 Alloy 718 Pipe Fittings supplier with high quality and Reasonalble Price.
Nickel Alloy Inconel 718 Pipe And Fittings Microstructure-Process-Property Relationship
The microstructure of Inconel 718 exhibits high sensitivity to hot processing techniques, with its mechanical properties directly influenced by the precipitation and dissolution dynamics of key phases (e.g., γ” precipitates). By precisely controlling thermal parameters such as temperature and deformation rates, the alloy’s phase evolution can be tailored to optimize strength, fatigue resistance, and structural stability
This sensitivity enables the development of customized heat treatment protocols (e.g., solution treatment and aging) to balance microstructural homogeneity and performance. Such process flexibility allows Inconel 718 to meet diverse engineering demands—from high-strength aerospace components to corrosion-resistant oilfield equipment—by adjusting grain boundary behavior and precipitate distribution
Nickel Alloy Inconel 718 Pipes And Fittings domestic and foreign counterparts Grade:
CN GB | USA UNS | Germany SEW VDIUV | UK BS | France AFNOR | |
Inconel 718 | GH4169 | N07718 | W.Nr.2.4668 NiCr19Fe19Nb5Mo3 | NA 51 | NC19FeNb |
Nickel Alloy Inconel 718 Pipes And Fittings Supply Specifications:
Round bar, bar, strip, pipe, seat, spheres, flanges and forgings
Nickel Alloy Inconel 718 Pipes And Fittings Chemical composition:
Alloy | C | Mn | Si | P | S | Cr | Ni | Mo | Cu | Ti | Al | Fe | 其他 |
Inconel 718 | ≤0.08 | ≤0.35 | ≤0.015 | ≤0.35 | ≤0.015 | 17 ~21 | 50 ~55 | 2.8 ~3.3 | ≤0.3 | 0.65 ~1.15 | 0.2 ~0.8 | margin | Nb 4.75~5.5 B≤0.006 Co≤1 |
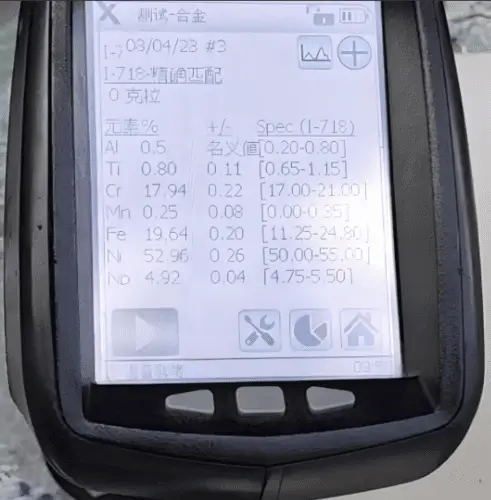
ASTM B670 UNS N07718 Nickel Alloy Inconel 718 Pipes and Fittings Suppliers and Manufacturers in china, Contact Us to Get Quotation of ASTM B366 UNS N07718 Alloy 718 Pipe Fittings supplier with excellent quality and Reasonalble Price.
Nickel Alloy Inconel 718 Pipes And Fittings Physical properties:
Density | 8.2g/cm3 |
Melting Point | 1260-1340℃ |
Nickel Alloy Inconel 718 Pipes And Fittings The minimum mechanical properties of alloys at room temperature:
Alloy | T S Rm N/mm2 | Y S RP0.2N/mm2 | Elongation A5 % | Brinell hardness HB |
Solution | 965 | 550 | 30 | ≤363 |
Nickel Alloy Inconel 718 Pipes And Fittings has the following features:
1. Easy processing
2. High tensile strength, fatigue strength, creep resistance and breaking strength at 700 ℃
3. High oxidation resistance at 1000 ° C
4. Stable chemical properties at low temperatures
5. Good welding performance
Nickel Alloy Inconel 718 Pipes And Fittings metallographic structure:
718 alloy is austenitic structure, and the γ-phase formed by precipitation hardening has excellent mechanical properties, and the δ phase generated at the grain boundary during the heat treatment has the best plasticity.
Nickel Alloy Inconel 718 Pipes And Fittings corrosion resistance:
Whether in high temperature or low temperature environment, 718 alloy has excellent resistance to stress cracking and pitting ability. 718 alloy in the high temperature oxidation resistance is particularly good.
Nickel Alloy Inconel 718 Pipes And Fittings Thermal processing performance and requirements:
Thrmal Processing
The appropriate hot working temperature is 1120-900 ℃, the cooling method can be water quenching or other rapid cooling method, after hot processing should be promptly annealed to ensure the best performance. Heat treatment materials should be heated to the upper limit of processing temperature, in order to ensure the plastic processing, deformation of 20% of the final processing temperature should not be less than 960 ℃.
Nickel Alloy Inconel 718 Pipes & fittings Cold working process performace and requirements:
cold working
The cold working should be carried out after the solution treatment, the work hardening rate is greater than the austenitic stainless steel, so the processing equipment should be adjusted accordingly, and in the cold process should be intermediate annealing process
Nickel Alloy Inconel 718 Pipes And Fittings welding process
Alloy with a satisfactory welding performance, available argon arc welding, electron beam welding, seam welding, spot welding and other methods of welding.
Inconel718 parts heat treatment process
Heat treatment of aerospace parts is usually carried out according to the standard heat treatment system and the direct aging heat treatment system.
What Nickel Alloy 718 Pipe Fittings Available For Production with KCM SPECIAL STEEL?
- Elbows: butt weld: 45degree, 90degere, 180 degree / Socket weld: 45 degree 90degree
- Tee: Butt weld: equal tee, reducing tee / Socket weld type is also available.
- Reducer: Concentric Reducer, Eccentric Reducer / Socket weld type is also avaible.
- Cap: butt weld and socket weld
- Cross: 4 ways pipe cross
- Stub End
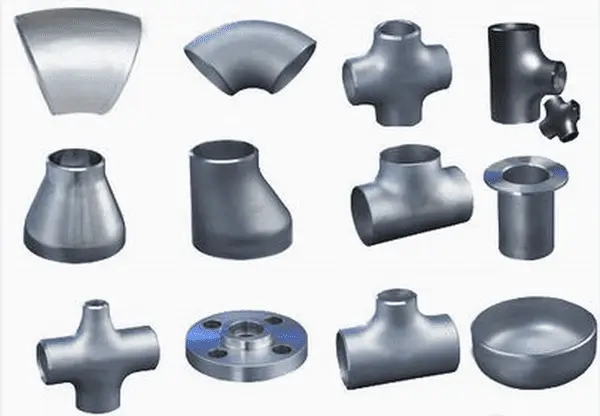
ASTM B670 UNS N07718 Nickel Alloy Inconel 718 Pipes and Fittings Supplier and Manufacturer in china, Contact Us to inquiry us ASTM B366 UNS N07718 Alloy 718 Pipe Fittings supplier with excellent quality and Reasonalble Price.
Customer Case Studies and Feedback on Nickel Alloy Inconel 718 Pipes and Fittings
Case Study 1: Aerospace Component Manufacturer
Customer Overview:
A leading aerospace component manufacturer specializing in high-performance engine parts approached KCM SPECIAL STEEL for Nickel Alloy Inconel 718 Pipes and Fittings. With stringent requirements for strength, fatigue resistance, and creep resistance at elevated temperatures, the manufacturer needed a reliable supplier who could meet their exacting specifications.
Requirement:
The customer required custom-made Inconel 718 pipes and fittings for turbine blades and other critical engine components. The materials had to withstand temperatures up to 700°C while maintaining excellent mechanical properties and corrosion resistance.
Solution Provided by KCM SPECIAL STEEL:
KCM SPECIAL STEEL offered precision-engineered Inconel 718 pipes and fittings, adhering strictly to ASTM B670 UNS N07718 standards. The company utilized its advanced manufacturing capabilities to produce complex-shaped components with superior microstructural stability and mechanical performance. The materials were subjected to customized heat treatments to optimize precipitation phases and ensure optimal strength and fatigue resistance.
Customer Feedback:
“We were impressed by KCM SPECIAL STEEL’s commitment to quality and precision. The Inconel 718 pipes and fittings delivered exceeded our expectations in terms of mechanical properties and corrosion resistance. The ability to customize heat treatments to meet our specific application needs was a game-changer. Our engine components now perform better and last longer, thanks to KCM SPECIAL STEEL’s expertise in nickel alloy materials.”
— Aerospace Component Manufacturer
Case Study 2: Nuclear Energy Plant Operator
Customer Overview:
A nuclear energy plant operator sought reliable Nickel Alloy Inconel 718 Pipes and Fittings for use in high-temperature, high-pressure environments within the plant’s reactor systems. The operator required materials with exceptional resistance to radiation, oxidation, and corrosion, combined with good weldability and processability.
Requirement:
The customer needed Inconel 718 pipes and fittings in various sizes and shapes, including elbows, tees, reducers, and caps, to accommodate the complex layout of the reactor systems. The materials had to meet strict safety regulations and be suitable for long-term service in nuclear applications.
Solution Provided by KCM SPECIAL STEEL:
KCM SPECIAL STEEL provided a comprehensive range of Inconel 718 pipes and fittings, tailored to the customer’s exact specifications. The company ensured compliance with all relevant safety standards and regulations, and offered detailed technical support throughout the procurement process. The materials were rigorously tested for mechanical properties, corrosion resistance, and weldability to guarantee performance reliability.
Customer Feedback:
“KCM SPECIAL STEEL’s expertise in nickel alloy materials and commitment to safety standards were crucial factors in our decision to partner with them. The Inconel 718 pipes and fittings delivered met our stringent requirements for radiation resistance, corrosion resistance, and processability. The technical support provided by KCM SPECIAL STEEL was invaluable in ensuring that our reactor systems were installed and operated safely and effectively. We look forward to continuing our collaboration with KCM SPECIAL STEEL for future projects.”
— Nuclear Energy Plant Operator
Case Study 3: Oil and Gas Exploration Company
Customer Overview:
An oil and gas exploration company needed Nickel Alloy Inconel 718 Pipes and Fittings for downhole equipment and other critical components exposed to extreme temperatures and corrosive environments. The company required materials with high tensile strength, fatigue strength, and creep resistance to ensure the reliability and durability of their equipment.
Requirement:
The customer specified Inconel 718 pipes and fittings for various downhole tools and components, including high-pressure valves, tubing, and connectors. The materials had to withstand temperatures up to 700°C and demonstrate excellent resistance to stress cracking and pitting corrosion.
Solution Provided by KCM SPECIAL STEEL:
KCM SPECIAL STEEL supplied custom-made Inconel 718 pipes and fittings, designed to withstand the harsh conditions encountered in oil and gas exploration. The company utilized its extensive experience in nickel alloy materials to ensure that the delivered products met the customer’s stringent requirements for mechanical properties and corrosion resistance. The materials were also tested for weldability and ease of processing to facilitate efficient manufacturing and installation processes.
Customer Feedback:
“KCM SPECIAL STEEL’s Inconel 718 pipes and fittings have proven to be an excellent choice for our downhole equipment. The materials have demonstrated outstanding performance in terms of strength, corrosion resistance, and weldability. The custom-made solutions provided by KCM SPECIAL STEEL allowed us to optimize the design and performance of our equipment, reducing downtime and maintenance costs. We highly recommend KCM SPECIAL STEEL to any company looking for reliable nickel alloy materials for oil and gas applications.”
— Oil and Gas Exploration Company
Frequently Asked Questions (FAQ) – Nickel Alloy Inconel 718 Pipes and Fittings
1. What is Inconel 718, and why is it used for pipes and fittings?
Answer:
Inconel 718 is a nickel-chromium-based superalloy renowned for its exceptional high-temperature strength, corrosion resistance, and creep resistance. It contains additives like niobium, molybdenum, and titanium, which enhance its mechanical properties through age-hardening. These characteristics make it ideal for manufacturing pipes and fittings in industries such as aerospace, oil and gas, nuclear energy, and chemical processing, where components face extreme temperatures, pressure, and corrosive environments.
2. What industries commonly use Inconel 718 pipes and fittings?
Answer:
Inconel 718 pipes and fittings are widely used in:
- Aerospace: For turbine blades, engine components, and exhaust systems.
- Oil & Gas: In downhole tools, valves, and high-pressure tubing for harsh drilling environments.
- Nuclear Energy: For reactor cooling systems, fuel rod cladding, and radiation-resistant components.
- Chemical Processing: In reactors, heat exchangers, and piping systems handling corrosive chemicals.
- Power Generation: For gas turbines, boilers, and steam generators operating at elevated temperatures.
3. How does Inconel 718 perform in high-temperature applications?
Answer:
Inconel 718 retains mechanical stability and oxidation resistance at temperatures up to 700°C (1292°F). Its unique microstructure, strengthened by gamma double prime (γ”) precipitates, prevents deformation under prolonged stress. This makes it suitable for high-temperature piping systems, exhausts, and heat exchangers where thermal fatigue and creep resistance are critical.
4. Can Inconel 718 pipes and fittings be customized?
Answer:
Yes! At KCM SPECIAL STEEL, we offer custom-engineered solutions tailored to your project requirements. Our capabilities include:
- Precision machining of complex shapes (elbows, tees, reducers).
- Customized heat treatments to optimize strength and corrosion resistance.
- Sizes and thicknesses tailored to specific pressure and temperature needs.
- Compliance with international standards such as ASTM B670, ASME SB670, and NACE MR0175.
5. What certifications and quality checks ensure the reliability of your products?
Answer:
We adhere to stringent quality assurance protocols:
- Material Certifications: Mill Test Reports (MTRs) validate chemical composition and mechanical properties.
- Non-Destructive Testing (NDT): Ultrasonic testing, radiography, and dye penetrant inspection detect flaws.
- Dimensional Checks: Precision measurement to ensure compliance with engineering specifications.
- Third-Party Audits: Independent verification of compliance with ISO 9001 and API Q1 standards.
6. How does Inconel 718 compare to stainless steel or other nickel alloys?
Answer:
- Stainless Steel: Inconel 718 outperforms stainless steel in high-temperature strength and corrosion resistance, especially in chloride-rich or acidic environments.
- Inconel 625: While Inconel 625 offers better resistance to pitting and crevice corrosion, Inconel 718 excels in mechanical strength and creep resistance due to its age-hardening properties.
- Hastelloy: Hastelloy alloys are superior in highly oxidizing environments, but Inconel 718 is more cost-effective for applications requiring high tensile strength and thermal stability.
7. What are the welding and fabrication considerations for Inconel 718?
Answer:
Inconel 718 requires specialized welding techniques to avoid cracking and maintain corrosion resistance:
- Pre-Weld Heat Treatment: Stress relief to minimize residual stresses.
- Post-Weld Heat Treatment (PWHT): Aging at 720°C to restore mechanical properties.
- Filler Metals: Use matching Inconel 718 filler wire (e.g., ERNiFeCr-2) for optimal results.
- Gas Shielding: Argon or helium shielding gases prevent oxidation during TIG or MIG welding.
8. How do I maintain Inconel 718 pipes and fittings for long-term performance?
Answer:
- Regular Inspections: Check for signs of corrosion, erosion, or thermal fatigue.
- Cleaning: Use alkaline or non-chlorinated solvents to remove contaminants. Avoid abrasive tools.
- Avoid Overheating: Ensure operating temperatures remain within the alloy’s design limits.
- Documentation: Track maintenance schedules and performance data for predictive upkeep.
9. What is the typical lead time for Inconel 718 pipe orders?
Answer:
Lead times vary based on order complexity:
- Standard Sizes: 4–6 weeks for pre-inventoried materials.
- Custom Orders: 8–12 weeks for specialized machining, heat treatments, and testing.
We prioritize urgent requests for critical projects while ensuring strict adherence to quality standards.
10. Why should I choose KCM SPECIAL STEEL for Inconel 718 pipes and fittings?
Answer:
KCM SPECIAL STEEL is a trusted global supplier with:
- Technical Expertise: Over 20 years of experience in nickel alloy manufacturing.
- End-to-End Solutions: From material selection to post-sale technical support.
- Global Compliance: Products meet ASME, ASTM, EN, and PED standards.
- Proven Track Record: Successful deployments in aerospace, nuclear, and oil & gas sectors (see customer case studies).
Summary: Why Inconel 718 Pipes and Fittings Are a Smart Investment
Inconel 718 pipes and fittings are engineered to deliver unmatched performance in the world’s most demanding industrial applications. Here’s why they stand out:
1. Superior Material Properties
- High-Temperature Stability: Maintains tensile strength and oxidation resistance up to 700°C.
- Corrosion Resistance: Resists pitting, crevice corrosion, and stress-corrosion cracking (SCC) in acidic, chloride, and H2S environments.
- Age-Hardenable: Achieves exceptional mechanical properties through tailored heat treatments.
2. Versatility Across Industries
From aerospace turbines to nuclear reactors, Inconel 718’s adaptability makes it a go-to material for engineers. Case studies highlight its success in:
- Aerospace: Enhancing engine component lifespan under extreme thermal cycling.
- Nuclear Energy: Ensuring safety and longevity in radiation-heavy reactor systems.
- Oil & Gas: Reducing downtime in corrosive drilling and extraction environments.
3. Cost-Effectiveness Over Time
While the initial cost of Inconel 718 is higher than standard alloys, its durability and low maintenance requirements result in significant long-term savings. Reduced replacements, downtime, and repair costs make it a value-driven choice for critical infrastructure.
4. Customization and Compliance
KCM SPECIAL STEEL’s ability to deliver custom solutions ensures that every project meets precise operational demands. Our adherence to international standards guarantees compliance with safety and performance regulations, whether for offshore oil rigs or aerospace prototypes.
5. Sustainability and Safety
Inconel 718’s long service life aligns with sustainable manufacturing goals by minimizing waste. Its reliability in high-risk environments also enhances workplace safety, particularly in nuclear and chemical processing plants.
Final Thoughts
Inconel 718 pipes and fittings are not just components—they are mission-critical assets that ensure operational efficiency, safety, and profitability. Whether you’re designing a next-gen aircraft engine or upgrading a nuclear reactor, partnering with KCM SPECIAL STEEL guarantees access to premium materials, technical expertise, and industry-proven solutions.