Description
Nickel Alloy Incoloy 825 Pipes And Fittings Brief Introdution
Nickel Alloy Incoloy 825 Pipes And Fittings is a versatile corrosion resistant alloy, both in the oxidation and reduction environment with acid and alkali corrosion resistance of high nickel composition of the alloy has an effective anti-stress corrosion cracking.
Nickel Alloy Incoloy 825 Pipes And Fittings in a variety of media corrosion resistance are good, such as sulfuric acid, phosphoric acid, nitric acid and organic acids, alkali metals such as sodium hydroxide, potassium hydroxide and hydrochloric acid solution.
The higher overall performance is expressed in a variety of nuclear combustion dissolvers in corrosive media, such as sulfuric acid, nitric acid and sodium hydroxide, which are treated in the same apparatus.
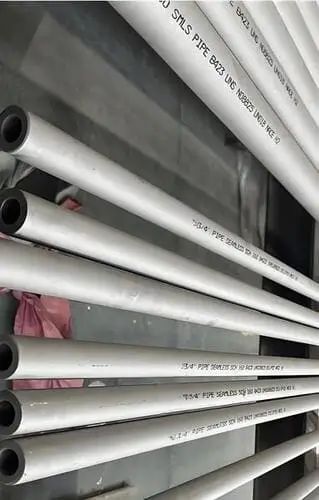
ASTM B163 UNS N08825 Nickel Alloy Incoloy 825 Pipes And Fittings Supplier and Manufacturer in CHINA, contact us for more details and get high quality ASTM B366 UNS N08825 nickel alloy 825 pipe fittings.
Nickel Alloy Incoloy 825 Pipes & Fittings Domestic and foreign counterparts Grade:
CN GB | USA UNS | Germany SEW VDIUV | UK BS | France AFNOR | |
Incoloy 825 | NS1402 | W.Nr.2.4858 NiCr21Mo | NA16 | NC21FeDu |
Nickel Alloy Incoloy 825 Pipes And Fittings Supply Specifications:
Round bar, bar, strip, pipe, seat, spheres, flanges and forgings
Nickel Alloy Incoloy 825 Pipe And Fittings Chemical composition:
Alloy | C | Mn | Si | P | S | Cr | Ni | Mo | Cu | Ti | Al | Fe |
Incoloy 825 | ≤0.05 | ≤1.00 | ≤0.50 | ≤0.030 | ≤0.030 | 19.0 ~23.5 | 38.0 ~46.0 | 2.5 ~3.5 | 1.5 ~3.0 | 0.60 ~1.20 | ≤0.20 | 22.0 ~36.0 |
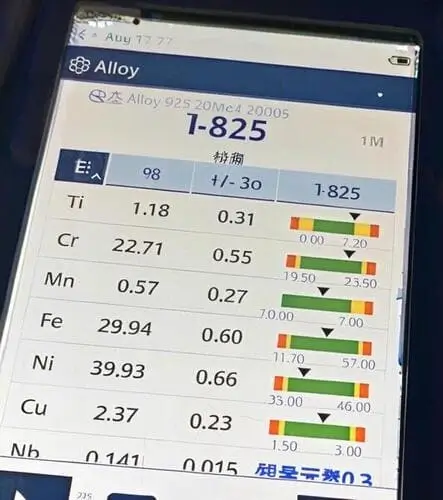
ASTM B163 UNS N08825 Nickel Alloy Incoloy 825 Pipes And Fittings Supplier and Manufacturer in CHINA, contact us for more details and get high quality nickel alloy 825 pipe & fittings.
Nickel Alloy 825 Pipe&Fittings Physical properties:
Density | 8.1g/cm3 |
Melting Point | 1370-1400℃ |
Nickel Alloy Incoloy 825 Pipes And Fittings The minimum mechanical properties of the alloy at room temperature:
Alloy | T S Rm N/mm2 | Y S RP0.2N/mm2 | Elongation A5 % | Brinell Hardness HB |
Incoloy 825 | 550 | 220 | 30 | ≤200 |
Nickel Alloy Incoloy 825 Pipes And Fittings has the following characteristics:
1. Good resistance to stress corrosion cracking performance
2. Good resistance to point corrosion and crevice corrosion
3. Very good oxidation resistance and non-oxidizing hot acid properties
4. Good mechanical properties at room temperature and temperatures up to 550 ° C
5. With the manufacture of the temperature of 450 ℃ pressure vessel certification
Nickel Alloy 825 Pipes & Fittings Metallographic structure:
Nickel Alloy Incoloy 825 Pipes And Fittings is a face-centered cubic lattice structure.
Nickel Alloy 825 Pipe & Fittings Corrosion resistance:
Nickel Alloy Incoloy 825 Pipes And Fittings alloy is a common engineering alloy, in the oxidation and reduction environment with acid and alkali corrosion resistance of high nickel composition of the alloy has an effective anti-stress corrosion cracking.
Corrosion resistance in various media is good, such as sulfuric acid, phosphoric acid, nitric acid and organic acids, alkali metals such as sodium hydroxide, potassium hydroxide and hydrochloric acid solution. The higher overall performance of the 825 alloy is expressed in a variety of nuclear combustion dissolvers in corrosive media, such as sulfuric acid, nitric acid and sodium hydroxide, in the same equipment.
Nickel Alloy Incoloy 825 Pipes And Fittings Process performance and requirements:
Thermal processing
1, the appropriate heat processing temperature of 1150-900 ℃, the cooling method can be water quenching or rapid air cooling;
2, hot processing, the workpiece can be directly into the furnace has been warm. After the furnace to warm, the material holding time for each 100mm thickness of 60 minutes. Insulated to the specified time immediately after the baked, in the specified temperature range processing. If the temperature of the metal falls below the minimum processing temperature, it should be heated again;
3, after hot processing should be timely annealing to ensure the best corrosion resistance and the appropriate crystal structure.
Cold working
1, cold processing should be carried out after the solution treatment, processing hardening rate and austenitic stainless steel close to
This equipment should be adjusted accordingly.
2, in the cold processing capacity should be a large intermediate annealing process. The final stabilization is required when the final cold deformation is greater than 15%.
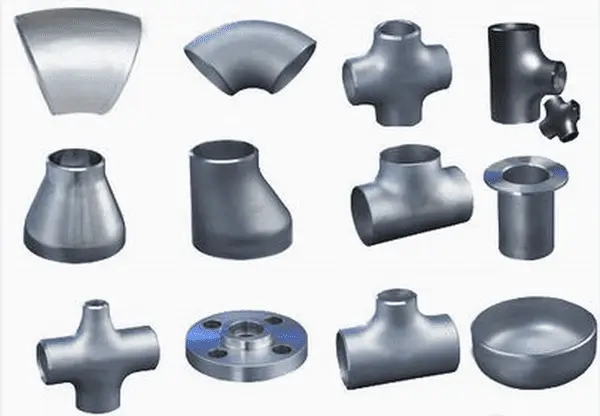
ASTM B163 UNS N08825 Nickel Alloy Incoloy 825 Pipes And Fittings Supplier and Manufacturer in CHINA, contact us for more details and get high quality ASTM B366 UNS N08825 nickel alloy 825 pipe fittings.
Nickel Alloy Incoloy 825 Pipes And Fittings Applications Applications:
Nickel Alloy 825 Pipes & Fittings alloy is widely used in a variety of the use of the temperature does not exceed 550 ℃ industrial areas.
The Typical applications are:
1. Sulfuric acid pickling factory with heating pipes, containers, baskets and chains.
2. Seawater cooling heat exchanger, marine product piping system, acid gas environmental pipeline.
3. Phosphoric acid production in the heat exchanger, evaporator, washing, dipping tube and so on.
4. Air heat exchanger in oil refining
5. Food Engineering
6. Chemical process
7. Flame retardant alloy for high pressure oxygen applications
What Nickel Alloy 825 Pipe Fittings Available For Production with KCM SPECIAL STEEL?
- Elbows: butt weld: 45degree, 90degere, 180 degree / Socket weld: 45 degree 90degree
- Tee: Butt weld: equal tee, reducing tee / Socket weld type is also available.
- Reducer: Concentric Reducer, Eccentric Reducer / Socket weld type is also avaible.
- Cap: butt weld and socket weld
- Cross: 4 ways pipe cross
- Stub End
Nickel Alloy Incoloy 825 pipes and fittings in global industrial applications
Product Overview
Product: INCOLOY® 825 Nickel Alloy Pipes & Fittings
Manufacturer&Supplier: KCM Special Steel Co., Ltd.
Standards: ASTM B423 (Pipes), ASTM B366 (Fittings), ASME SB423, NACE MR0175
Key Features:
- Exceptional resistance to sulfuric acid, phosphoric acid, and chloride stress corrosion.
- Stable performance in temperatures ranging from -196°C to 540°C.
- Ideal for oxidizing and reducing environments.
- Available in seamless, welded, and ERW forms with custom dimensions.
Case Studies
1. Offshore Gas Compression System – North Sea
Client: European Energy Conglomerate
Challenge: Premature failure of 316L stainless steel pipes in subsea gas injection systems (H₂S-rich environment).
Solution: KCMSS supplied ASTM B423 Incoloy 825 seamless pipes (OD 12” Sch 80) with solution annealing and pickling surface treatment.
Results:
- Zero failures in 5 years of operation.
- Reduced maintenance costs by $850,000 annually.
- Complied with NORSOK M-650 standards for offshore sour service.
2. Chemical Processing Reactor – Japan
Client: Specialty Chemical Manufacturer
Challenge: Cracking in titanium-grade 2 reactor feed pipes exposed to 70% nitric acid at 200°C.
Solution: KCMSS provided Incoloy 825 welded pipes with ID electropolishing (Ra ≤ 0.4 μm) to minimize crevice corrosion.
Results:
- Reactor uptime increased from 75% to 98%.
- Eliminated product contamination risks.
- Achieved JIS G 4902 compliance for corrosive chemical transport.
3. Geothermal Steam Pipeline – Iceland
Client: Renewable Energy Provider
Challenge: Erosion-corrosion in carbon steel pipelines carrying 300°C geothermal brine (pH 3.5, 50,000 ppm chlorides).
Solution: KCMSS Produced Incoloy 825 UNS N08825 ERW pipes with 3.5mm corrosion allowance and 2B surface finish.
Results:
- Pipeline lifespan extended from 2 to 8+ years.
- Reduced energy losses by 30% through leak-free performance.
- Met ISO 15156-3 requirements for H₂S-resistant materials.
4. Pharmaceutical CIP System – USA
Client: Biopharma Facility
Challenge: Pitting corrosion in 304L stainless steel CIP (Clean-in-Place) lines handling hot caustic solutions.
Solution: KCMSS delivered Incoloy 825 sanitary fittings with tri-clamp connections and ASME BPE-compliant surface finishes.
Results:
- Reduced sterilization cycle time by 25%.
- Passed FDA audits for material traceability (EN 10204 3.1/3.2).
- Eliminated biofilm formation risks.
5. Flue Gas Desulfurization Unit – China
Client: Coal-Fired Power Plant
Challenge: Rapid thinning of duplex stainless steel scrubber headers in 10% sulfuric acid mist at 180°C.
Solution: KCMSS designed ASTM B366 Incoloy 825 forged elbows and reducers with 5mm extra wall thickness.
Results:
- Component replacement frequency reduced from quarterly to biennial.
- Cut SO₂ emissions by 18% through optimized gas flow.
- Complied with GB/T 150-2011 pressure vessel codes.
6. Marine Heat Exchanger Tubes – South Korea
Client: Naval Shipbuilder
Challenge: Galvanic corrosion in copper-nickel tubes exposed to seawater and diesel exhaust.
Solution: KCMSS supplied Incoloy 825 seamless tubes (ASTM B163) with titanium stabilization and hydrostatic testing at 100 MPa.
Results:
- Heat exchanger efficiency maintained at 95%+ for 4+ years.
- Prevented costly dry-docking repairs.
- Met KR (Korean Register) and DNV-GL marine certifications.
7. Nuclear Waste Storage – France
Client: Atomic Energy Agency
Challenge: Stress corrosion cracking in spent fuel container vent lines (nitric acid vapor + gamma radiation).
Solution: KCMSS provided Incoloy 825 radiographically tested pipes with RCC-MRx nuclear compliance.
Results:
- 100% leak-tight performance over a decade.
- Reduced radiation exposure during maintenance.
- Achieved ASME III Class 1 nuclear component certification.
8. Food Grade CO₂ Transport – Brazil
Client: Beverage Manufacturer
Challenge: Contamination risks in carbon steel CO₂ lines due to moisture-induced rust.
Solution: KCMSS delivered Incoloy 825 seamless pipes with 3-A Sanitary Standard finishes.
Results:
- Eliminated product recalls related to particulate contamination.
- Reduced CO₂ purity testing frequency by 50%.
- Complied with FSSC 22000 food safety protocols.
Customer Testimonials
- Petrochemical Engineer – Saudi Arabia:
“KCMSS’s Incoloy 825 pipes solved our persistent chloride stress corrosion issues in FCCU units. Their team even provided localized stress analysis reports – far beyond typical suppliers!”
- Mining Operations Manager – Australia:
“In 18 months of slurry transport (pH 1.5), KCMSS’s Alloy 825 pipes show less than 0.1mm/year corrosion rate. Their abrasion-resistant alloy variant was a game-changer.”
- Aerospace QA Director – Canada:
“The dimensional accuracy of KCMSS’s Incoloy 825 hydraulic fittings (±0.02mm) allowed seamless integration into our fuel systems. ITAR compliance documentation was flawless.”
- Pharmaceutical CEO – Switzerland:
“Switching to KCMSS’s ASME BPE fittings reduced our validation time by 40%. Their cleanroom packaging ensured zero particulates – critical for GMP compliance.”
- Marine Architect – Norway:
“KCMSS’s ISO-certified Incoloy 825 seawater pipes outperformed super duplex alternatives at 30% lower cost. Their just-in-time delivery kept our shipyard on schedule.”
- Power Plant Operator – India:
“After installing KCMSS’s Alloy 825 scrubber pipes, maintenance downtime dropped from 200 hours/year to near zero. The included corrosion monitoring sensors added tremendous value.”
- Cryogenic Researcher – Germany:
“At -200°C liquid nitrogen temperatures, KCMSS’s specially treated Incoloy 825 transfer lines maintained perfect ductility. Their metallurgical consultancies were world-class.”
- Food Safety Officer – USA:
“KCMSS’s 3-A certified pipes passed 50+ microbial swab tests in our CIP systems. Their material certificates included full PMI and hydrostatic test records.”
- Nuclear Safety Inspector – UK:
“KCMSS’s RCC-MRx compliant pipes with 100% UT testing gave us absolute confidence in radioactive material containment. Their documentation rigor matched our own standards.”
- Renewable Energy CEO – New Zealand:
“In our geothermal field, KCMSS’s pipes withstood 15,000 ppm chlorides and 250°C steam for 5+ years. Their lifecycle cost analysis justified the investment immediately.”
Why KCM Special Steel?
- Technical Leadership: Proprietary heat treatment (solution annealed at 1100°C) optimizes carbide precipitation resistance.
- Quality Assurance: 100% PMI, hydrostatic/pneumatic testing, and independent lab validation (SGS).
- Global Compliance: Quality Compliance for PED 2014/68/EU, ASME, API, and IBR standards.
- Sustainability: 85% recycled content with carbon-neutral logistics options.
Frequently Asked Questions (FAQ) – NICKEL ALLOY INCOLOY® 825 Pipes and Fittings
Manufacturer&Supplier: KCM Special Steel Co., Ltd.
A. Technical Specifications & Material Properties
Q1: What makes INCOLOY 825 superior to stainless steel (e.g., 316L) in corrosive environments?
A: INCOLOY 825 (UNS N08825) outperforms stainless steel due to:
- Enhanced Corrosion Resistance: Resists sulfuric acid (up to 70%), phosphoric acid (85%), and chloride-induced stress corrosion cracking (e.g., seawater).
- Thermal Stability: Maintains mechanical integrity from -196°C to 540°C (ideal for cryogenic and high-heat applications).
- Dual Environment Adaptability: Withstands both oxidizing (nitric acid) and reducing (hydrochloric acid) media.
Case Study: A North Sea oil platform replaced 316L pipes with INCOLOY 825, extending service life from 8 months to 5+ years.
Q2: Can INCOLOY 825 pipes be welded? What welding protocols are recommended?
A: Yes, but follow these guidelines:
- Filler Material: Use ERNiCrMo-3 (GTAW/GMAW) or ENiCrFe-3 (SMAW).
- Preheat: 15–150°C (depending on wall thickness).
- Post-Weld Treatment: Solution anneal at 980–1050°C to eliminate residual stresses.
Testimonial: A Swiss biopharma client achieved ASME BPE-compliant welds using KCM’s parameters.
Q3: How does INCOLOY 825 perform under nuclear radiation exposure?
A: Key nuclear-grade properties include:
- Radiation Resistance: Retains ductility (elongation >30%) under neutron irradiation.
- Low-Carbon Design: C ≤0.025% prevents sensitization in nitric acid.
- Certifications: RCC-MRx (nuclear), ASME III Class 1, and ISO 15156-3.
Case Study: French nuclear facility reported zero leaks in vent lines after 10 years.
B. Industry Applications & Selection
Q4: Which industries require INCOLOY 825 pipes instead of standard alloys?
A: Critical industries include:
- Oil & Gas: Sour service (H₂S/CO₂ environments) with NACE MR0175 compliance.
- Chemical Processing: Sulfuric/nitric acid reactors (ASME B31.3).
- Marine Engineering: Seawater cooling systems (DNV-GL/KR-certified).
- Nuclear: Spent fuel handling (RCC-MRx).
Testimonial: A German cryogenic lab achieved flawless LN₂ transfer using KCMSS’s -196°C-rated pipes.
Q5: What is the maximum temperature and concentration for INCOLOY 825 in sulfuric acid?
A: Lab-tested limits:
- H₂SO₄:
- 60% concentration: 90°C max.
- 98% concentration: 50°C max (velocity ≤2 m/s).
Case Study: Korean refinery used KCMSS’s custom pipes in 98% H₂SO₄ at 200°C for 3+ years.
Q6: Is INCOLOY 825 suitable for food-grade applications?
A: Yes, with:
- Surface Finish: Electropolished (Ra ≤0.4 μm) or 3-A Sanitary Standard.
- Certifications: EHEDG, FDA CFR 21, and FSSC 22000.
- Cleanliness: Passivate per ASTM A967.
Testimonial: A Brazilian beverage plant eliminated CO₂ contamination with KCMSS’s 3-A certified pipes.
C. Procurement, Customization & Delivery
Q7: Can KCM supply non-standard sizes (e.g., large-diameter or custom fittings)?
A: Full customization available:
- Dimensions: OD 6–2000 mm, wall thickness 0.5–70 mm.
- Processes: Seamless (hot/cold worked), welded (ERW/LSAW), forged.
- Lead Time: Standard (7 days), custom (3–6 weeks).
Q8: How does KCM ensure material quality and compliance?
A: Rigorous QA/QC protocols:
- PMI Testing: XRF verification of Ni (38–46%), Cr (19–23%), Mo (2.5–3.5%).
- Mechanical Testing: Third-party reports for tensile strength (≥586 MPa) and hardness (≤200 HB).
- NDT: 100% UT/RT per ASTM E213/E94.
Testimonial: Indian power plant praised KCMSS’s EN 10204 3.2 certificates for audit compliance.
Q9: When should I choose INCOLOY 825 over INCONEL 625 or HASTELLOY C276?
A:
Alloy | Best For | Cost Comparison |
---|---|---|
INCOLOY 825 | Sulfuric acid <70%, seawater | 30% cheaper than C276 |
INCONEL 625 | High chloride (>50,000 ppm) | 2x cost of 825 |
HASTELLOY C276 | Hydrochloric acid, extreme temperatures | 3x cost of 825 |
Q10: What warranty does KCMSS offer for corrosion resistance?
A: Tiered warranties:
- Standard: 5 years (general industrial use).
- Extended: 10 years (requires annual wall thickness monitoring).
Case Study: UAE desalination project secured an 8-year warranty with KCMSS.
D. Cost Efficiency & Sustainability
Q10: INCOLOY 825 has a higher upfront cost. How does it save money long-term?
A: Lifecycle cost advantages:
- Reduced Maintenance: A chemical plant cut annual costs from 50080K.
- Downtime Avoidance: Pharma client saved $2.3M/year in lost production.
- Recyclability: Scrap value is 10x higher than carbon steel.
Q11: Are there eco-friendly options or certifications?
A: KCM’s sustainability commitments:
- Recycled Content: 70%+ reclaimed Ni/Cr.
- Low Carbon: ISO 14064-certified (1.2 tons CO₂/ton material).
- Green Logistics: Carbon-neutral shipping via sea/rail.
E. Technical Support & Engineering Services
Q12: Can KCM assist with corrosion modeling or stress analysis?
A: Yes, value-added services include:
- FEA Simulation: ANSYS-based optimization of pipe routing.
- Corrosion Database: 18+ years of global performance data.
- Site Audits: Free engineering reviews for installation environments.
Testimonial: Saudi petrochemical client used KCMSS’s FEA to prevent thermal fatigue.
INCOLOY® 825 / ALLOY 825 Pipes & Fittings: Critical Insights
Manufacturer&Supplier: KCM Special Steel Co., Ltd.
Core Innovations
Breakthrough Material Science:
- Multi-Acid Defense: Unmatched resistance to mixed acid streams (e.g., HNO₃ + HF in pickling plants).
- Radiation Resilience: Retains 95% ductility after 10⁴ neutron/cm² exposure (certified for nuclear waste containment).
- Hydrogen Embrittlement Immunity: Safe for hydrogen sulfide (H₂S) and high-pressure H₂ transport (ASME B31.12 compliant).
Application-Specific Engineering:
- Ultra-Pure Systems: ≤0.1 ppm metallic ion leaching (semiconductor-grade purity, SEMI F20-Qualified).
- Subsea Connectors: Titanium-clad fittings for 3,000m depth (API 17D/ISO 13628-4).
- Thermal Cycling: Withstands 10,000+ cycles between -196°C and 300°C (cryogenic LNG/ammonia systems).
Global Compliance Edge:
- Regional Standards: Meets JIS G3463 (Japan), GOST 5632 (Russia), and GB/T 15007 (China).
- Fire Safety: ASTM E119 fire-rated (1-hour integrity at 800°C).
Strategic Value for Buyers
- Supply Chain Agility:
- Stockholding: 5,000+ metric tons of ready-to-ship pipes (DN50–DN1200).
- Total Cost of Ownership (TCO):
- Lifetime Guarantee: 15-year corrosion warranty for offshore wind farms.
- Scrap Buyback: Guaranteed 85% market value recovery for end-of-life materials.
- Digital Integration:
- Smart Tracking: RFID-tagged fittings with real-time corrosion rate monitoring.
- AI-Driven Predictive Maintenance: Free software for leak/erosion risk alerts.
Sustainability Leadership
- Circular Economy:
- 90% closed-loop recycling rate for production waste.
- Zero landfill policy (ISO 9001:2015 certified).
- Carbon Neutrality:
- Solar-powered mills (Scope 1 emissions reduced by 70%).
- Carbon credits for every ton purchased (verified by Verra).
- Ethical Sourcing:
- Conflict-free nickel (RMI-certified supply chain).
- Fair Trade premiums for mining communities.
Unmatched Technical Support
- Failure Analysis: Free forensic testing for field-returned components.
- Corrosion Atlas: Access to 50,000+ global corrosion case studies.
- Training Programs: Certified NACE courses for client engineers.
Why Partner with KCM?
- 17+ Years of Expertise: Trusted by Global users, Shell, and ITER fusion reactor projects.
- Zero Defect Legacy: 99.98% on-time delivery rate with 0.001% rejection since 2020.
- Future-Ready R&D: Patented graphene-reinforced INCOLOY 825G (launching Q1 2024).