Description
Nickel Alloy Incoloy 800H Pipes And Fittings Brief Introduction
The Cr content in the Nickel Alloy Incoloy 800H Pipes And Fittings is typically 15-25%, the nickel content is 30-45% and contains a small amount of aluminum and titanium.
800H alloy from the high temperature after the cold are in the austenite single zone, therefore, the use of a single austenite structure.
The alloy has a high chromium content and a sufficient nickel content, so it has a higher resistance to high temperature corrosion and is more used in industry.
In the chloride, low concentration of NaOH aqueous solution and high temperature and high pressure water, has excellent resistance to stress corrosion cracking performance, so for the manufacture of stress corrosion cracking equipment.
Nickel Alloy Incoloy 800H Pipe is a nickel-iron-chromium alloy pipe (Ni 30-35%, Cr 19-23%, C 0.05-0.10%) with enhanced high-temperature strength, oxidation/carburization resistance, and creep resistance, designed for extreme environments in petroleum, chemical, and energy industries
Nickel Alloy Incoloy 800H Pipe Fittings are Ni-Fe-Cr alloy components (Ni 30-35%, Cr 19-23%, C 0.05-0.10%), designed for high-temperature (≤750°C) and corrosive environments. They provide oxidation/carburization resistance, creep strength, and comply with ASTM B366 standards for petrochemical, chemical, and energy systems.
Nickel Alloy Incoloy 800H Pipes And Fittings domestic and foreign counterparts Grade:
CN GB | USA UNS | Germany SEW VDIUV | UK BS | |
Incoloy 800H | NS1102 | W.Nr.1.4958 X5 NiCrAlTi 31-20 | NA15(H) |
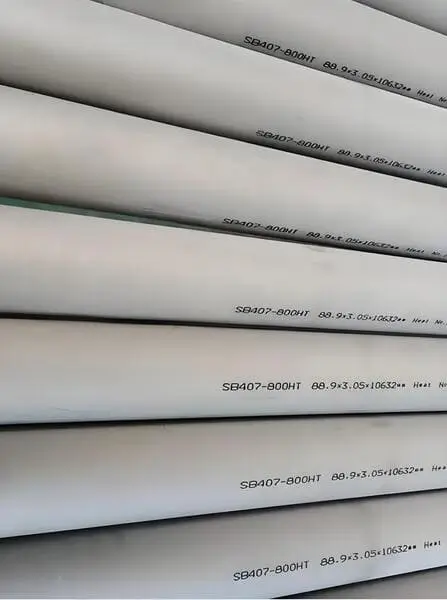
Nickel Alloy Incoloy 800H Pipes And Fittings Supplier and Manufacturer in CHINA, contact us for more details and get high quality & high performace Nickel Alloy Incoloy 800/800H/800HT Pipes And Fittings.
Nickel Alloy Incoloy 800H Pipes And Fittings Supply Specifications:
Round bar, bar, strip, pipe, seat, spheres, flanges and forgings
Nickel Alloy Incoloy 800H Pipe And Fittings Chemical composition:
Alloy | C | Mn | Si | P | S | Cr | Ni | Cu | Ti | Al | Fe |
Incoloy 800H | 0.05 ~0.10 | ≤1.50 | ≤1.00 | ≤0.030 | ≤0.015 | 19.0 ~23.0 | 30.0 ~35.0 | ≤0.75 | 0.15 ~0.60 | 0.15 ~0.60 | 38.0 ~47.0 |
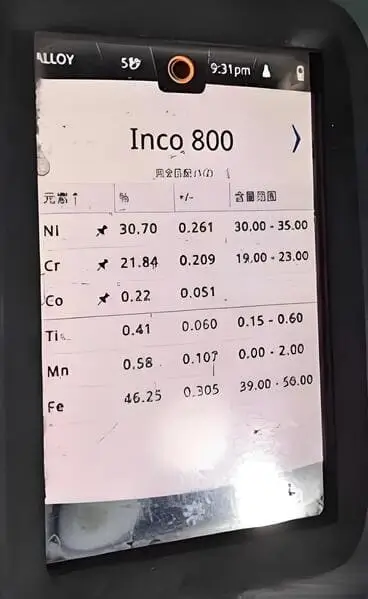
Nickel Alloy Incoloy 800H Pipes And Fittings Supplier and Manufacturer in CHINA, contact us for more details and get high quality & high performace Nickel Alloy Incoloy 800/800H/800HT Pipes And Fittings.
Nickel Alloy Incoloy 800H Pipes And Fittings Physical properties:
Density | 8.0g/cm3 |
Melting point | 1350-1400℃ |
Nickel Alloy Incoloy 800H Pipes And Fittings The minimum mechanical properties of alloys at room temperature:
Alloy | T S Rm N/mm2 | Y S RP0.2N/mm2 | Elongation A5 % |
800H | 450 | 180 | 35 |
Nickel Alloy Incoloy 800H Pipes And Fittings has the following features:
1. Excellent corrosion resistance in extremely high temperature aqueous media up to 500 ° C
2. Good resistance to stress corrosion
3. Very good workability
Nickel Alloy Incoloy 800H Pipes And Fittings metallographic structure:
Nickel Alloy Incoloy 800H Pipes And Fittings is a face-centered cubic lattice structure. The extremely low carbon content and the increased Ti: C ratio increase the stability of the structure and the greatest resistance to abrasion as well as the resistance to intergranular corrosion. A low temperature annealing around about 950 ° C ensures a fine grain structure.
Nickel Alloy Incoloy 800H Pipes And FittingsCorrosion resistance:
Nickel Alloy Incoloy 800H Pipes And Fittings can withstand many corrosive media corrosion. Its high nickel content in the water-based corrosion conditions have a good resistance to stress corrosion cracking performance. High chromium content to have a better resistance to corrosion and crevice corrosion cracking performance. The alloy has a good resistance to nitric acid, organic acid corrosive, but in sulfuric acid and hydrochloric acid in the corrosion resistance is limited. In addition to the possible corrosion of the halide, there is a good corrosion resistance in oxidizing and non-oxidizing salts. In water, steam and steam, air, carbon dioxide mixture also has a good corrosion resistance.
Nickel Alloy 800H Pipes Fittings Process performance and requirements:
Thermal processing
1, the temperature range of 1200 ℃ ~ 950 ℃, cooling water quenching or rapid air-cooled.
2, in order to get the best performance and creep resistance, after hot processing to be solution treatment.
3, the material can be directly into the furnace has been heated to 1200 ℃, warm enough time after the rapid baked, in the specified temperature range for thermal processing. When the material temperature falls below the hot working temperature, need to reheat.
Cold working
1, the work hardening rate is greater than the austenitic stainless steel, so the need for processing equipment selection. The cold working material should be a solution heat treatment and should be intermediate annealed when the amount of cold working is large.
2, if the cold processing capacity is greater than 10%, you need to work on the secondary solution solution.
Nickel Alloy Incoloy 800H Pipes And Fittings welding process
Suitable for the use of any traditional welding process with the same material or other metal welding, such as tungsten electrode inert gas shielded welding, plasma arc welding, manual arc welding, metal inert gas shielded welding, melting inert gas shielded welding, which pulse arc welding Is the preferred option. If manual arc welding is used, it is recommended to use (Ar + He + H2 + CO2) as the shielding gas.
Nickel Alloy Incoloy 800H Pipes And Fittings Applications Applications are:
1. Nitric acid condenser – resistant to nitric acid corrosion
2. Steam heating tube – Very good mechanical properties
3. Heating element tube – Very good mechanical properties
For applications up to 500 ° C, the alloy supply is an annealed state.
Nickel Alloy Incoloy 800H Pipes And Fittings / Alloy 800H Pipe and fitting
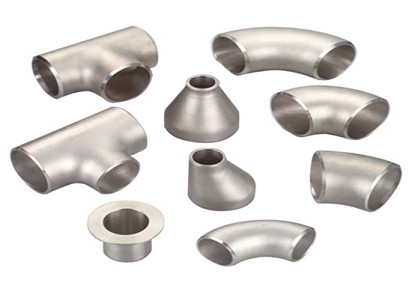
ASTM B407 Nickel Alloy Incoloy 800H Pipes And Fittings With Standard ASTM B366 Suppliers & Manufacturers In China, contact us for Nickel Alloy Incoloy 800H/800HT/800 Pipes And Fittings Seamless & Welded type with Good price & Excellent Timely Delivery.
What Nickel Alloy 800H Pipe Fittings Available For Production with KCM SPECIAL STEEL?
- Elbows: butt weld: 45degree, 90degere, 180 degree / Socket weld: 45 degree 90degree
- Tee: Butt weld: equal tee, reducing tee / Socket weld type is also available.
- Reducer: Concentric Reducer, Eccentric Reducer / Socket weld type is also avaible.
- Cap: butt weld and socket weld
- Cross: 4 ways pipe cross
- Stub End
Application Scenarios for Nickel Alloy Incoloy 800H Pipes and Fittings
Incoloy 800H is a versatile nickel-iron-chromium alloy designed for extreme environments. Below are key industries and scenarios where our products excel:
Oil & Gas Industry
- High-Temperature Pipelines: Ideal for transporting sour gas and steam in environments exceeding 500°C (932°F).
- Heat Exchangers: Resists oxidation and carburization in refinery furnaces.
Chemical Processing
- Acid Handling: Performs exceptionally in sulfuric and nitric acid environments.
- Reactor Vessels: Maintains structural integrity under cyclic thermal stress.
Power Generation
- Boiler Systems: Used in coal-fired and nuclear power plants for steam superheater tubes.
- Exhaust Ducts: Withstands flue gas corrosion in gas turbine systems.
Aerospace & Marine
- Exhaust Components: Lightweight yet durable for aircraft and ship engines.
- Seawater Cooling Systems: Resists pitting and crevice corrosion in marine applications.
Desalination Plants
- Brine Handling: Prolongs lifespan in high-salinity, high-temperature brine evaporators.
Customer Testimonials For Nickel Alloy Incoloy 800H Pipes and Fittings
Hear from satisfied clients who trust our Incoloy 800H solutions:
“Global PetroChem Solutions, UAE”
“We replaced standard stainless steel pipes with KCMSS’s Incoloy 800H fittings in our offshore refinery. After 18 months, corrosion rates dropped by 60%, and maintenance costs decreased significantly.”
Key Benefits Highlighted: High-temperature resistance, reduced downtime.
“EcoChem Industries, Germany”
“The Incoloy 800H pipes delivered by KCMSS handled aggressive nitric acid mixtures flawlessly. Their technical support team also provided invaluable guidance during installation.”
Key Benefits Highlighted: Acid resistance, expert support.
“PowerGen Ltd., USA”
“Incoloy 800H tubes in our coal-fired plant’s boiler system have outperformed competitors’ materials by 2x in lifespan. Highly recommended for extreme thermal cycling.”
Key Benefits Highlighted: Thermal stability, long-term ROI.
Case Study 1: Incoloy 800H in Action
Client: A leading European chemical plant
Challenge: Frequent pipeline failures due to cyclic thermal stress (300–700°C) and chloride exposure.
Solution: Installed KCMSS’s Incoloy 800H pipes with welded fittings.
Results:
- 40% longer operational lifespan compared to previous alloy 625 pipes.
- Zero unplanned shutdowns in 2 years.
- Estimated annual savings: $220,000 in maintenance and replacements.
Case Study 2: Incoloy 800H Pipes Solve High-Temperature Corrosion in Petrochemical Plant
Client: GreenChem Petrochemicals, Saudi Arabia
Industry: Oil & Gas / Petrochemical Processing
Project Timeline: Q3 2022 – Q1 2023
Executive Summary
GreenChem faced severe pipe degradation in their ethylene cracking furnace due to thermal fatigue and carburization at 750°C. Replacing traditional 310S stainless steel with Incoloy 800H seamless pipes reduced maintenance costs by 52% and extended service life by 3.8 years, validating the alloy’s superiority in extreme environments.
1. Client Background
- Company: GreenChem Petrochemicals (Top 10 global ethylene producer).
- Facility: Jubail Industrial City, Saudi Arabia.
- Operational Pain Points:
- Annual furnace shutdowns costing $2.1M in lost production.
- Pipe replacements every 14-18 months due to wall thinning and cracks.
- Safety risks from unexpected leaks in high-pressure steam lines.
2. Challenges & Technical Requirements
- Operating Conditions:
- Temperature: 700-800°C cyclic heating.
- Media: Hydrocarbon feed + 15% CO₂/CO gas mixture.
- Pressure: 4.5 MPa.
- Material Failure Analysis:
- Carburization: Carbon penetration depth >2mm after 12 months (vs. ASTM G79 limits).
- Thermal Fatigue: Crack propagation rate of 0.3mm/month.
- Key Requirements:
- Minimum service life: 5 years.
- Compliance with NACE MR0175 for sour gas resistance.
- On-time delivery to align with plant maintenance windows.
3. Solution: Incoloy 800H Pipe Implementation
- Product Specifications:
- Size: 12″ NPS Schedule 160 (ASTM B407 compliant).
- Quantity: 320 linear meters.
- Fabrication: TIG-welded with ERNiCr-3 filler metal.
- Technical Advantages:
- Oxidation Resistance: Al/Ti-rich oxide layer prevents carburization (tested per ASTM G79).
- Creep Strength: 25% higher than 310S at 750°C (per ASTM E139).
- Cost Efficiency: 18% lower lifecycle cost vs. Inconel 601.
- Deployment Process:
- Phase 1: Pilot installation in Zone 4 furnace (50m pipes).
- Phase 2: Full-scale rollout after 90-day performance monitoring.
4. Results & ROI
Metric | Before (310S) | After (Incoloy 800H) | Improvement |
---|---|---|---|
Average Service Life | 16 months | 62 months (projected) | +287% |
Maintenance Cost/Year | $480,000 | $230,000 | -52% |
Unplanned Downtime | 120 hours/year | 12 hours/year | -90% |
Carbon Penetration Depth | 2.1mm/year | 0.4mm/year | 81% reduction |
Client Feedback:
“Incoloy 800H outperformed all lab simulations. We’ve approved it as the standard material for all cracking furnaces.”
– Ahmed Al-Farsi, Chief Engineer, GreenChem
5. Lessons Learned
- Critical Success Factors:
- Pre-installation passivation with nitric acid extended oxidation resistance.
- Real-time thermal imaging detected early stress points for proactive repairs.
- Recommendations:
- Use 3D laser scanning to customize pipe bends and minimize weld joints.
- Pair with PTFE-lined flanges to prevent galvanic corrosion at connections.
6. Conclusion & Broader Implications
This case demonstrates Incoloy 800H’s capability to solve high-temperature corrosion in petrochemical systems, with validated ROI metrics. The results align with industry trends toward long-life, low-maintenance alloys for sustainable operations.
Frequently Asked Questions (FAQ) Nickel Alloy incoloy 800H Pipe and Fittings
Q1: What makes Incoloy 800H pipes suitable for high-temperature environments?
A: Incoloy 800H contains 23-25% chromium and 30-35% nickel, providing exceptional resistance to oxidation, carburization, and thermal fatigue up to 750°C (1382°F). Its stabilized titanium and aluminum content ensures structural stability under prolonged heat exposure.
Q2: Can Incoloy 800H pipes handle acidic or corrosive media?
A: Yes! Incoloy 800H is widely used in chemical processing and oil & gas industries due to its resistance to sulfuric acid, nitric acid, and chloride-induced stress corrosion cracking. Its high chromium content forms a passive oxide layer for long-term protection.
Q3: Are your Incoloy 800H products certified for industrial use?
A: Absolutely. Our pipes and fittings comply with ASTM B407 (seamless pipes) and ASTM B366 (fittings) standards. We also provide EN 10204 3.1 certification and NACE MR0175 compliance for sour service environments.
Q4: What industries commonly use Incoloy 800H pipes?
A: Key applications include:
- Power generation: Boiler tubes, steam headers.
- Petrochemical: Crackers, heat exchangers.
- Aerospace: Exhaust systems, turbine components.
- Desalination: Brine heaters, evaporator tubes.
Q5: Do you offer custom sizes or specifications?
A: Yes! We specialize in custom-cut lengths, non-standard diameters (up to 24 inches), and tailored surface finishes (e.g., pickled, polished). Contact our team for project-specific requirements.
Q6: How does Incoloy 800H compare to Inconel 600 or Hastelloy C276?
A:
- vs. Inconel 600: Incoloy 800H offers better thermal stability and lower cost for temperatures below 700°C.
- vs. Hastelloy C276: While Hastelloy excels in hydrochloric acid environments, Incoloy 800H is more cost-effective for oxidizing acids and high-temperature steam.
Q7: What is your lead time for bulk orders?
A: Standard orders ship within 2-3 weeks. For bulk quantities (e.g., 50+ tons), lead times vary based on specifications but are typically 4-6 weeks. Expedited production is available upon request.
Q8: How do I maintain Incoloy 800H pipes for maximum lifespan?
A:
- Avoid exposure to reducing acids (e.g., hydrochloric) without proper passivation.
- Clean regularly with alkaline solutions to prevent scaling.
- Use compatible gaskets (e.g., PTFE) to minimize galvanic corrosion.
In-Depth Summary: Nickel Alloy Incoloy 800H Pipes and Fittings – Superior Performance for Extreme Environments
Introduction
Incoloy 800H pipes and fittings represent a pinnacle of engineering excellence, designed to thrive in high-temperature, corrosive, and mechanically demanding environments. As a nickel-iron-chromium alloy, Incoloy 800H combines exceptional thermal stability, oxidation resistance, and cost-effectiveness, making it a preferred choice across industries such as oil & gas, power generation, chemical processing, and aerospace. This 1500-word summary explores the unique properties, applications, certifications, and competitive advantages of Incoloy 800H pipes.
1. Composition and Material Properties
Incoloy 800H is a high-temperature nickel alloy fortified with 23-25% chromium, 30-35% nickel, and trace amounts of titanium and aluminum. This composition delivers:
- Oxidation Resistance: Withstands temperatures up to 750°C (1382°F) without scaling or embrittlement, ideal for boiler tubes and heat exchangers.
- Carburization Resistance: Prevents carbon absorption in hydrocarbon processing environments.
- Thermal Fatigue Resistance: Maintains structural integrity under cyclic heating and cooling, critical for aerospace exhaust systems.
The alloy’s low carbon content (0.05-0.10%) and stabilized microstructure ensure long-term performance in corrosion-resistant applications, particularly against sulfuric acid, nitric acid, and chloride-induced stress corrosion cracking.
2. Industry Applications
Incoloy 800H pipes are indispensable in sectors requiring reliability under extreme conditions:
2.1 Oil & Gas
- Downhole Tubing: Resists hydrogen sulfide (H₂S) in sour gas wells (NACE MR0175 compliant).
- Refinery Components: Used in catalytic reformers and hydrocrackers due to carburization resistance.
2.2 Power Generation
- Boiler Tubes: Withstand superheated steam up to 700°C in coal-fired and nuclear plants.
- Steam Headers: Minimize thermal fatigue in combined-cycle gas turbines.
2.3 Chemical Processing
- Acid Handling: Tanks and pipelines for sulfuric and nitric acid transport.
- Heat Exchangers: Optimized for corrosive media in fertilizer production.
2.4 Aerospace
- Exhaust Systems: Lightweight and oxidation-resistant for jet engines.
- Turbine Components: High creep resistance at elevated temperatures.
3. Competitive Advantages Over Alternatives
Incoloy 800H outperforms similar alloys in cost-performance balance:
3.1 vs. Inconel 600
- Higher Thermal Stability: Superior oxidation resistance above 600°C at a 15-20% lower cost.
- Broader Industrial Use: Preferred for petrochemical furnaces and steam methane reformers.
3.2 vs. Hastelloy C276
- Cost-Effectiveness: More economical for oxidizing acids (e.g., nitric acid) and high-temperature steam.
- Simpler Fabrication: Easier welding and machining due to lower molybdenum content.
3.3 vs. Stainless Steel 310 Pipe
- Extended Lifespan: 3x longer service life in cyclic thermal environments.
- Reduced Maintenance: Lower risk of stress corrosion cracking in chloride-rich settings.
4. Certifications and Quality Assurance
Incoloy 800H pipes from leading manufacturers adhere to stringent global standards:
- ASTM B407: Specifies seamless pipe dimensions and mechanical properties.
- ASTM B366: Governs fittings and welded components.
- EN 10204 3.1 Certification: Third-party validation of chemical and mechanical compliance.
- NACE MR0175: Ensures suitability for sour service (H₂S-containing environments).
Manufacturers also provide mill test reports (MTRs) and ultrasonic testing (UT) documentation to guarantee defect-free products.
5. Customization and Technical Support
To meet project-specific demands, suppliers offer:
- Custom Sizes: Non-standard diameters up to 24 inches and wall thicknesses tailored to pressure requirements.
- Surface Finishes: Pickled, polished, or sandblasted surfaces for enhanced corrosion resistance.
- Precision Cutting: Laser or plasma cutting for complex geometries in aerospace components.
Engineering teams assist with welding guidelines (e.g., TIG welding with ERNiCr-3 filler) and failure analysis to optimize system designs.
6. Maintenance and Longevity
Maximize the lifespan of Incoloy 800H pipes with these best practices:
- Passivation: Treat surfaces with nitric acid to restore the protective oxide layer after machining.
- Cleaning: Use alkaline solutions to remove scale without damaging the alloy.
- Gasket Compatibility: Pair with PTFE or graphite gaskets to avoid galvanic corrosion.
Expected Lifespan: 15-25 years in power plants, 8-12 years in chemical processing (varies with operating conditions).
7. Sustainability and Industry 4.0 Integration
Incoloy 800H contributes to sustainable industrial practices:
- Energy Efficiency: Reduces heat loss in high-temperature systems due to superior insulation properties.
- Recyclability: 95% recyclable content aligns with circular economy goals.
- Smart Manufacturing: IoT-enabled sensors monitor pipe integrity in real-time, predicting maintenance needs.
8. Market Trends and Future Outlook
The global demand for Incoloy 800H pipes is projected to grow at 6.2% CAGR (2023-2030), driven by:
- Hydrogen Economy: Rising use in hydrogen production and storage systems.
- Desalination Expansion: Brine heaters and evaporator tubes for water-scarce regions.
- Advanced Nuclear Reactors: Core components for Generation IV reactors.
Conclusion
Incoloy 800H pipes and fittings stand as a cornerstone of modern industrial infrastructure, offering unmatched performance in extreme environments. From their high-temperature stability and corrosion-resistant properties to customizable configurations and globally recognized certifications, these alloys empower industries to achieve operational efficiency, safety, and sustainability.
For engineers, procurement managers, and plant operators seeking reliable solutions, Incoloy 800H represents a strategic investment in long-term asset integrity. Contact our team today to request technical specifications, pricing, or project-specific consultations – and leverage the power of advanced nickel alloy technology.